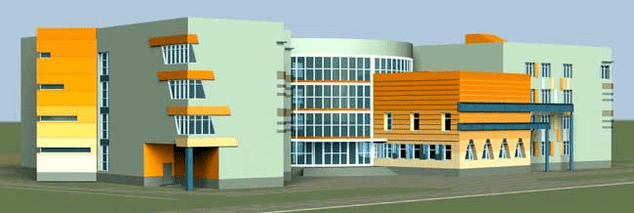
Economia de energia na empresa - as principais direções:
- Economizando energia elétrica
- Redução de perdas de calor e vapor
- Redução de perdas em linhas de vapor
Economia de energia na empresa - Métodos de economia de energia
- Seleção da categoria de preço ideal e revisão dos termos contratuais de fornecimento de energia
- Otimização de motores elétricos
- Instalação VFD
- Otimizando sistemas de ar comprimido
Escolha da categoria de preço ideal para fonte de alimentação
No total, existem 6 categorias de preços de fornecimento de energia, segundo as quais as empresas podem comprar eletricidade de fornecedores garantidos.
Todos os pequenos empreendimentos com capacidade instalada inferior a 670 kW, no momento da celebração do contrato de fornecimento automático de energia, enquadram-se na primeira categoria de preços.
Todos os empreendimentos com capacidade instalada de mais de 670 kW se enquadram automaticamente na terceira categoria de preços.
A primeira e a terceira categorias de preço nem sempre são as categorias de fonte de alimentação mais ideais e mais baratas.
Em alguns casos, mudar para uma categoria de preço diferente pode reduzir o custo da eletricidade em 5% -30%.
O tópico de categorias de preços é bastante extenso, em nossa análise sobre categorias de preços, contamos em detalhes como calcular corretamente e escolher a categoria de preços da fonte de alimentação.
Além das categorias de preços, também recomendamos dar uma olhada em outros aspectos do contrato de fornecimento de energia:
- nível de tensão,
- potência,
- tarifa de transmissão de energia elétrica.
Em nossa análise, você pode descobrir mais sobre esses e outros métodos para reduzir os custos de energia.
Economia de energia na empresa - motores elétricos
É necessário levar em consideração todos os equipamentos onde são utilizados motores elétricos:
- bombas,
- compressores,
- fãs,
- máquinas-ferramentas,
- linhas de produção.
Plano de controle de motor elétrico
O plano de controle do motor deve se tornar uma parte integrante do programa de conservação de energia da planta.
Esse plano ajudará a implementar um sistema de economia de energia de longo prazo para todos os motores elétricos da empresa.
O plano de controle do motor irá garantir que falhas e malfuncionamentos não ocorram e, se ocorrerem, serão resolvidos de forma rápida e eficiente.
Passos para criar um plano de controle motor:
- Faça um inventário de todos os motores da instalação.
- Crie uma lista de motores com seus principais parâmetros, condição técnica e vida útil.
- Desenvolva instruções gerais para a realização de reparos.
- Desenvolver diretrizes para manutenção preventiva, lubrificação e inspeção.
- Crie um estoque de segurança de peças sobressalentes usadas com frequência.
- Crie uma especificação de compra para novos motores.
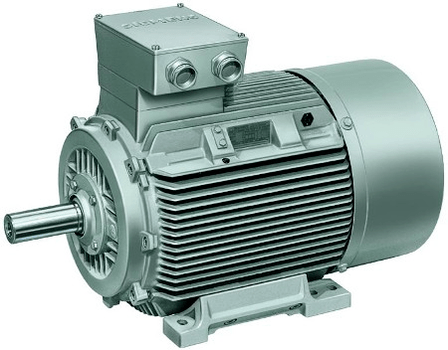
Rebobinando motores elétricos
Geralmente, rebobinar um motor elétrico antigo é muito mais barato do que comprar um novo.
O motor elétrico deve ser trocado se o custo de rebobinamento for superior a 60% do custo de um novo.
Então, tudo vai depender de como o retrocesso é realizado.
Se o trabalho for feito no nível mais alto, o motor perderá apenas 1% -2% de sua eficiência.
Se o rebobinamento for mal executado, as perdas no motor elétrico aumentarão em 5% -10%.
Substituir o motor elétrico antigo por um novo com eficiência energética faz sentido nos casos em que o motor funciona mais de 2. 000 horas por ano.
O período de retorno para um novo motor com eficiência energética não será superior a 1, 5 - 2 anos.
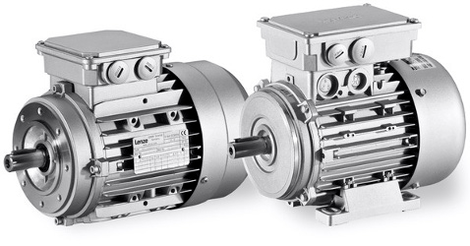
Economia de energia na empresa, aumentando o fator de carga
O fator de carga é a relação entre a potência operacional e a potência aparente.
É assim que a energia é usada de forma eficiente.
Quanto mais alto o fator de carga, mais eficientemente a eletricidade é usada.
O motor elétrico opera de maneira ideal com 75% da carga e acima.
Portanto, instalar motores acima da potência necessária (por motivos de segurança) não só será mais caro, mas também ineficiente em termos de consumo de energia.
O fator de carga pode ser aumentado da seguinte forma:
- desligamento de motores descarregados,
- substituição de motores, que são carregados em menos de 45%, por modelos menos potentes,
- redistribuição da carga entre os motores elétricos existentes.
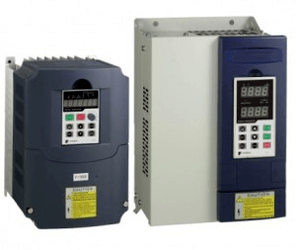
Unidade de frequência variável (VFD)
A instalação de drives de frequência variável só faz sentido para sistemas dinâmicos.
Em sistemas estáticos, que estão envolvidos, por exemplo, apenas para elevar cargas, a instalação de um conversor de frequência não ajudará e muitas vezes pode causar danos.
O VFD equilibra a carga e a velocidade do motor, garantindo assim o uso ideal da energia elétrica.
O VFD pode reduzir o consumo de energia do motor em um mínimo de 5% e um máximo de 60%.
O período de retorno para VFD é geralmente de 1-3 anos.
Otimização de sistemas de ar comprimido
O ar comprimido é usado em uma ampla variedade de indústrias.
Em algumas empresas, o ar comprimido é o principal consumidor de eletricidade.
O ar comprimido é utilizado em dispositivos e equipamentos pneumáticos, em transportadores, linhas automáticas.
O uso de ar comprimido é popular porque é uma fonte de energia conveniente e segura.
Mas muitas pessoas esquecem que o ar comprimido é uma das fontes de energia mais ineficientes - apenas 5% da eletricidade gasta na produção de ar comprimido se transforma em trabalho útil, os 95% restantes vão para a tubulação.
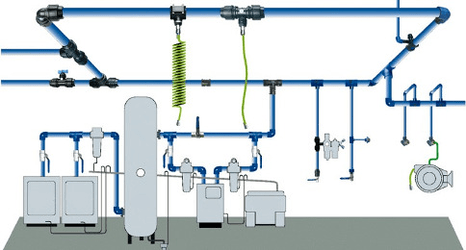
Economia de energia na empresa - ar comprimido:
- Não use ar comprimido para limpar as instalações.
- Reduzir a temperatura do ar na entrada do compressor em 3% reduz o consumo de energia em 1%.
- Para esses processos técnicos, sempre que possível, reduza a pressão do ar comprimido ao mínimo. Abaixar a pressão em 10% reduz o consumo de energia em 5%.
- Realize inspeções regulares, reparos em equipamentos de compressores e linhas de transmissão de ar comprimido. Um, mesmo o menor vazamento de ar comprimido, pode às vezes reduzir a eficiência do equipamento.
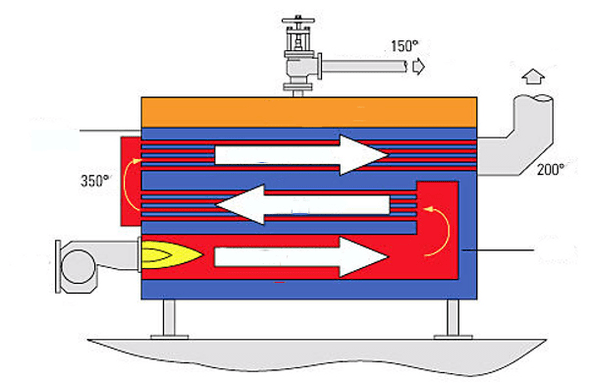
Economia de energia na empresa - reduzimos as perdas de calor e vapor
O vapor é frequentemente usado na indústria, especialmente nas indústrias têxtil, alimentícia e de processamento.
Melhorar a eficiência das caldeiras a vapor e reutilizar o calor gerado pode reduzir significativamente o consumo de energia nessas fábricas.
Produção de vapor
A caldeira funciona de forma mais eficiente na potência máxima.
Devido ao fato de que a demanda pela quantidade de vapor pode mudar ao longo do tempo, muitas vezes acontece que a caldeira trabalhe abaixo de sua carga ideal.
A capacidade da caldeira instalada pode ser muito superior às necessidades do empreendimento, devido à queda na demanda dos produtos ou planos não realizados de expansão da produção.
Além disso, a capacidade da caldeira pode não ser necessária devido a melhorias no processo de produção ou à introdução de medidas de economia de energia.
Nestes casos, a caldeira não funciona em plena capacidade ou em ciclos curtos de liga-desliga.
Ambas as situações acarretam perdas de energia significativas.
Não existem soluções simples e baratas para este problema.
A opção mais fácil éinstale uma "pequena" caldeira que funcione a plena capacidadecom uma carga de trabalho média ou baixa na empresa.
Apesar de não ser uma solução barata, o período de retorno desse investimento pode ser inferior a dois anos.
E, em geral, é sempre mais eficiente ter várias pequenas caldeiras intercambiáveis, especialmente em empresas com demanda variável ou flutuações sazonais significativas no consumo de calor e vapor.
Sistema de regulação automática
Se a empresa tiver várias caldeiras, faz sentido instalarsistema automático para regular a carga das caldeiras. . .
A automação responde à necessidade de vapor do empreendimento, redistribuindo a carga entre as caldeiras, liga ou desliga as caldeiras, aumentando significativamente a eficiência de todo o sistema.
Válvula de gaveta
Em empresas onde as caldeiras são desligadas regularmente devido a uma queda na demanda de vapor, as perdas de calor pela chaminé podem ser bastante altas.
É possível bloquear a perda de ar quente pela chaminéinstalando uma válvula de gavetaque fecha a tubulação quando a caldeira é desligada.
Prevenção e manutenção
Se não forem supervisionados, os queimadores e os sistemas de retorno de condensado podem se deteriorar ou falhar rapidamente.
Isso pode reduzir a eficiência da caldeira em 20% -30%.
Um programa de manutenção simples - garantindo que todos os componentes da caldeira estão operando em seu nível máximo - aumentará significativamente a eficiência operacional.
Na prática, a manutenção regular reduz o consumo de energia da caldeira em 10%.
Isolamento - a perda de calor da superfície de uma caldeira devidamente isolada deve ser inferior a 1%.
Remoção de fuligem e incrustações
É necessário monitorar e eliminar constantemente a formação de fuligem nos tubos da caldeira, incrustação no interior da caldeira.
Uma camada de fuligem com 0, 8 milímetros de espessura reduz a transferência de calor em 9, 5%, enquanto uma camada de 4, 5 milímetros de espessura reduz a transferência de calor em 69%!
As incrustações se formam quando o cálcio, a magnésia e o silício são depositados no trocador de calor da caldeira.
A escala de 1 milímetro de espessura aumenta o consumo de energia em 2%.
A fuligem e as incrustações podem ser removidas mecanicamente ou com ácidos.
A formação de fuligem e incrustações pode ser determinada por um aumento na temperatura dos gases de combustão ou por inspeção visual quando a caldeira não está em operação.
A formação de fuligem e incrustações deve ser monitorada com especial atenção se a caldeira funcionar com combustíveis sólidos (carvão, turfa, lenha).
Caldeiras a gás são menos propensas a problemas de fuligem.
Otimização da descarga da caldeira
A purga da caldeira é a descarga de água da caldeira para limpar a água de dentro da caldeira de impurezas e sais.
O objetivo da purga da caldeira é evitar ou reduzir a formação de incrustações.
A purga insuficiente da caldeira pode levar à entrada de água no vapor ou à formação de depósitos na caldeira.
A purga excessiva significa perda de calor, água e produtos químicos.
O nível de purga ideal depende do tipo de caldeira, da pressão operacional na caldeira, da preparação e da qualidade da água utilizada.
A primeira coisa a prestar atenção é a preparação da água. Se a água for bem tratada (baixo teor de sal), a taxa de purga pode ser de 4%.
Se houver substâncias estranhas e sais na água, a taxa de purga será de 8% -10%.
O sistema de purga automática também pode reduzir significativamente o consumo de energia.
O período de retorno para tal sistema é geralmente de 1-3 anos.
Redução das emissões de fumaça
A fumaça excessiva geralmente é o resultado da penetração de ar na caldeira e na chaminé por meio de vazamentos e aberturas.
Isso reduz a transferência de calor e aumenta a carga no sistema do compressor.
Vazamentos e furos podem ser facilmente eliminados, bastando fazer uma inspeção visual periódica da caldeira e da chaminé.
Regulação de ar
Quanto mais ar é usado para queimar combustível, mais calor é lançado ao vento.
Uma quantidade de ar ligeiramente acima da relação combustível / ar estequiométrica ideal é necessária por razões de segurança, para reduzir as emissões de NOx, e depende do tipo de combustível.
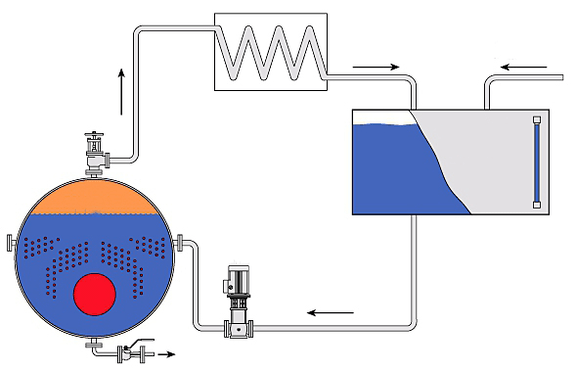
Caldeiras em más condições técnicas podem usar até 140% de ar adicional, resultando em emissões excessivas de combustão.
Um queimador de gás eficiente requer 2% a 3% de oxigênio suplementar, ou 10% a 15% de ar suplementar, para queimar o combustível sem gerar monóxido de carbono.
A regra geral é que a eficiência da caldeira aumenta em 1% para cada 15% de redução no ar adicional.
Portanto, é necessário verificar constantemente a relação combustível / ar.
Este evento não custa nada, mas tem um efeito muito bom.
Monitoramento de emissão de fumaça
A quantidade de oxigênio no gás de combustão é a soma do ar adicional (adicionado para aumentar a segurança e reduzir as emissões) e o ar que penetra na caldeira através de orifícios e vazamentos.
A presença de vazamentos e buracos pode ser facilmente detectada se um sistema de monitoramento do ar de entrada e da quantidade de oxigênio nos gases de combustão for estabelecido.
Utilizando os dados de quantidade de monóxido de carbono e oxigênio, é possível otimizar a relação combustível / ar na caldeira.
A instalação de um sistema de monitoramento e análise de emissões de combustão geralmente se paga em menos de um ano.
Economia de energia na empresa - instalando um economizador
O calor dos gases de combustão pode ser usado para aquecer a água que entra na caldeira.
A água aquecida entra na caldeira e requer menos calor para ser convertida em vapor, economizando combustível.
A eficiência da caldeira aumenta em 1% por cada diminuição de 22 ° C na temperatura dos gases de combustão.
O economizador pode reduzir o consumo de combustível em 5% - 10% e terá retorno em menos de 2 anos.
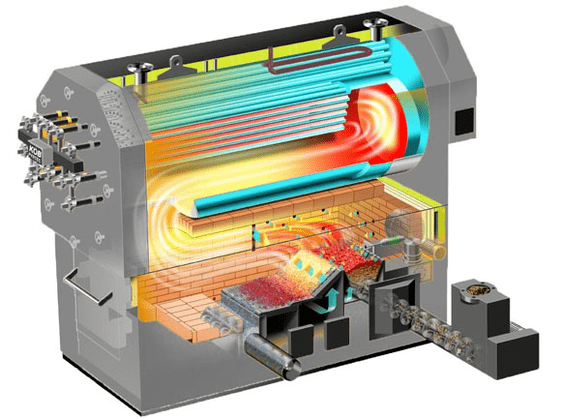
Trocador de calor para extrair calor da água e vapor da purga da caldeira
O trocador de calor ajudará a reciclar cerca de 80% da água e do calor do vapor da purga da caldeira.
Este calor pode ser utilizado para aquecer edifícios ou aquecer a água que alimenta a caldeira.
Qualquer caldeira com uma taxa de purga constante de 5% ou mais é uma excelente candidata para um trocador de calor.
Se o sistema de purga não operar em um modo constante, então faz sentido pensar em transferi-lo para um modo constante enquanto simultaneamente instala um trocador de calor.
O período de retorno médio para um trocador de calor não excederá 1, 5 - 2 anos.
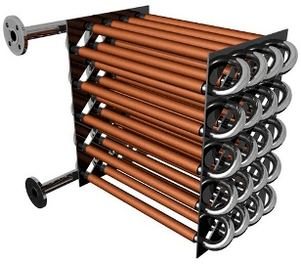
Instalando um economizador de condensação
O condensado quente pode retornar à caldeira, conservando energia e reduzindo a necessidade de água tratada.
O economizador de condensação pode aumentar a eficiência do sistema em mais 10%.
A instalação de tal economizador deve ser realizada sob a supervisão de especialistas que levarão em consideração todas as nuances de tal sistema, seu efeito na caldeira e a composição química da água.
Usar um sistema que retorna o condensado para a caldeira geralmente se paga em 1-1, 5 anos.
Um sistema que direciona o condensado para um suprimento de água quente se paga em menos de um ano.
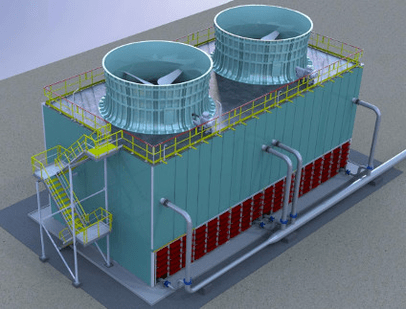
Torres de resfriamento (torres de resfriamento)
Uma torre de resfriamento é um trocador de calor no qual a água é resfriada por uma corrente de ar.
E em termos de eficiência energética, uma torre de resfriamento é um dispositivo que despeja calor para o vento.
Potencial de economia de energia em torres de resfriamento:
- Em algumas empresas, faz sentido abandonar totalmente as torres de resfriamento. Existem muitos casos em que o aquecimento é usado para aquecer uma sala e, ao mesmo tempo, uma torre de resfriamento é usada para dissipar o calor. A instalação de uma bomba de calor resolverá o problema de aquecimento e, pelo menos parcialmente, reduzirá a necessidade de usar a torre de resfriamento.
- A instalação de disjuntores para ventiladores da torre de resfriamento pode reduzir o consumo de energia em 40%.
- A substituição dos ventiladores de alumínio ou ferro por ventiladores novos (fibra de vidro e plástico moldado) pode reduzir o consumo de energia em até 30%.

Redução de perdas em linhas de vapor
Desconexão de linhas de vapor não reclamadas
As necessidades e o consumo de vapor mudam constantemente.
Isso pode levar ao fato de que todo o sistema de distribuição de vapor não é usado em capacidade total, mas apenas 20% -50%, o que inevitavelmente leva a perdas de calor.
É claro que otimizar ou reconfigurar todo o sistema de distribuição de vapor para atender às novas necessidades será muito caro e, talvez, inviável.
No entanto, identificar e desligar linhas de vapor que raramente são usadas pode ser uma medida de economia de energia muito eficaz.
Economia de energia na empresa - Isolamento térmico de tubulações
Os tubos de vapor isolantes podem reduzir as perdas de energia em até 90%.
Este é um dos retornos mais rápidos na economia de energia em um sistema de distribuição de vapor.
O período médio de retorno do investimento para o isolamento de dutos através dos quais o vapor ou água quente é transmitido é de cerca de 1 ano.
Tubos de condensado por 1, 5-2 anos.
Monitoramento de purgadores
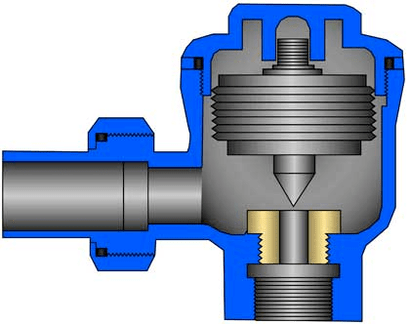
Um programa simples de monitoramento da condição técnica dos purgadores pode reduzir significativamente a perda de calor.
Por exemplo, se a manutenção não for realizada por 3 a 5 anos, então, como regra, cerca de um terço dos purgadores de vapor estão avariados, permitindo que o vapor escoe para o sistema de drenagem de condensado.
Na prática, em empreendimentos que possuem um programa de monitoramento de purgadores, no máximo 5% dos purgadores estão com defeito.
O período médio de retorno para a substituição ou manutenção de um purgador é de menos de seis meses.
Um programa de monitoramento de purgador normalmente reduzirá as perdas de vapor em 10%.
Purificadores de vapor termostáticos
O uso de purgadores termostáticos modernos pode reduzir o consumo de energia e, ao mesmo tempo, aumentar a confiabilidade de todo o sistema.
A principal vantagem dos purgadores termostáticos é que eles
- aberto quando a temperatura se aproxima do nível de vapor saturado (+/- 2 C °),
- emitem gases não condensáveis após cada abertura e
- estão no estado aberto no início da operação do sistema, o que garante seu rápido aquecimento.
Além disso, esses purgadores de vapor são muito confiáveis e podem ser usados em uma ampla gama de pressões.
Desconectando purgadores de vapor
Você pode reduzir o consumo de energia desligando os purgadores de vapor nas linhas de vapor superaquecido quando não estiverem em uso.
Eliminação de vazamentos de vapor
Um programa de reparo de vazamento de vapor em um pequeno orifício pode pagar em menos de 3 a 4 meses.
Não devemos esquecer que pequenos vazamentos podem passar despercebidos por anos, causando danos constantes ao sistema.
Reutilização de condensado e vapor
Quando um purgador de vapor descarrega condensado de um sistema de vapor, a queda de pressão cria vapor desse condensado.
Este vapor, junto com o condensado, pode ser usado em um trocador de calor para aquecer a água ou o ar.
Mais importante ainda, é possível usar esse vapor e condensado próximo ao ponto de liberação, pois pode ser muito caro criar um sistema de tubulação separado para transportá-lo até o ponto de uso.